Панацея роста: как производительность труда помогает в оптимизации бизнес-процессов
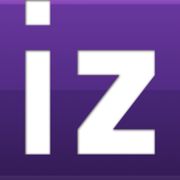

Почти треть российских компаний, опрошенных аналитиками Банка России, рассчитывают по итогам года увеличить производительность труда более чем на 6–15%. В условиях глобальной перестройки бизнес-процессов, увеличения объемов производств и дефицита персонала рост производительности становится универсальным инструментом повышения эффективности. Лидеры отраслей поняли это еще в начале 2000-х и стали внедрять собственные производственные системы. Одним из первых в стране такую модель построил автозавод в Нижнем Новгороде — именно его наработки лежат в основе современных методик.
Прогноз о росте производительности труда опубликован в мартовском докладе Банка России о развитии региональной экономики. Под производительностью регулятор понимает рост физического объема выпуска на одного работника. В среднем опрошенные компании ожидают в 2024 году увеличения этого показателя на 3,2%. Это медианная оценка в целом по экономике, а по ряду отраслей средние ожидания еще выше: например, в производстве инвестиционных товаров (оборудование, стройматериалы) предприятия рассчитывают на увеличение производительности на 4,2%, в производстве промежуточных товаров (сырье, комплектующие) — на 3,9%, в добыче ископаемых — на 3,8%. При этом почти 30% опрошенных компаний рассчитывают, что производительность труда в этом году вырастет на 6–15% и выше.
Задумываться о росте производительности предприятия стимулирует ситуация в экономике. По информации Центробанка, в IV квартале 2023 года уровень загрузки производственных мощностей достиг исторического максимума (81%): стараясь удовлетворить растущий спрос, компании увеличивали инвестиции и объемы производства. Новые рекорды бьют и показатели безработицы: 3,2% по итогам года — самый низкий за историю наблюдений (с 1992 года), а это значит, растет и дефицит кадров.
На эти факторы, выступая в конце года перед депутатами Госдумы, указывала глава Центробанка Эльвира Набиуллина.
— Сейчас мы находимся в ситуации, когда экономика практически полностью задействовала имеющиеся ресурсы. Это касается и рабочих рук, и производственных мощностей. Безработица в 3%, а в некоторых регионах и того меньше — это означает, что в экономике практически не осталось свободных рук. Ситуация с кадрами действительно очень острая, особенно в тех отраслях, которые перешагнули докризисный уровень. Например, в машиностроении и химической промышленности. (…) Для дальнейшего роста экономики РФ нужно повышение производительности труда, — отмечала глава Банка России
Ресурсы производительности
Главными факторами роста производительности опрошенные Центробанком компании называют оптимизацию производства и бизнес-процессов, увеличение квалификации сотрудников, увеличение загрузки сотрудников и введение в строй нового оборудования. Прежде всего речь идет об автоматизации и роботизации производственных линий.
Здесь нет ничего нового. Всё это — столпы производственных систем, которые российские компании сами или с помощью государства внедряют у себя на протяжении последних лет. С 2018 года в стране реализуется нацпроект «Производительность труда», в рамках которого менеджеров бесплатно консультируют о возможностях бережливых технологий, помогают оптимизировать логистику и бизнес-процессы. Его результаты впечатляют: на пилотных участках, с которых начинают обучение сотрудников и внедрение новых принципов, производительность растет на 20–40%.
За пять лет поддержку в рамках нацпроекта получило более 4 тыс. предприятий. По данным АНО «Национальные приоритеты», они смогли увеличить прибыль на 318 млрд рублей — выгода от принятых мер оказалась почти в 10 раз больше, чем бюджет нацпроекта. Очевидны и эффекты для рынка труда: по оценке главы Минэкономразвития Максима Решетникова, за шесть лет за счет роста производительности потребность экономики в кадрах снизилась на 100 тыс. человек. А если нацпроект продлят, то эффект к 2030 году перекроет более 10% кадрового дефицита в стране.
Универсальный ответ на вызовы
В основе современных методик по внедрению бережливых технологий — опыт российских компаний, которые начинали эту работу первыми. Среди них — автозавод в Нижнем Новгороде, куда еще в начале 2000-х по инициативе промышленника Олега Дерипаски прибыли приглашенные специалисты корпорации Toyota. Именно ее производственная система, придуманная еще в 1930-е годы, считается первоисточником для всех, возникших позднее.
— Главное отличие японской системы от, например, американской — прежде всего в том, что в первом случае во главе угла стоит развитие людей, а во втором — внедрение определенного комплекса инструментов и практик, — рассказывает директор по развитию производственной системы нижегородского автозавода Оксана Исакова.
При этом, по ее словам, у предприятия не было задачи копировать японскую систему — все принципы разрабатывались заново во время практической работы.
— Нам никто не давал готовых рецептов — консультанты задавали наводящие вопросы, а ответы и решения мы искали сами, на основе своего опыта и в реальных условиях производства. Свою производственную систему мы писали постепенно, и теперь это наша философия, которая лежит в основе всего, — продолжила Исакова.
Сегодня предприятие стабильно удерживает долю рынка — около 60% — в своем сегменте легких коммерческих грузовиков (LCV), не уступая китайским конкурентам. Обеспечить такие результаты удалось благодаря производственной системе, которая помогает гибко реагировать на все внешние вызовы, какими бы они ни были. Вне зависимости от контекста предприятие ежедневно работает над стандартизацией процессов, унификацией номенклатуры, над быстрой переналадкой оборудования, построением единичных потоков, качеством обратной связи и так далее. При этом процессы идут на всех уровнях: каждое подразделение, каждый цех, каждая бригада формируют свои стратегии развития и детальные планы на неделю, месяц, год.
В результате, если, например, в период кризиса 2008–2010 годов бережливые технологии позволили автозаводу эффективно сжать производство и оптимизировать процессы, то сейчас — наоборот, помогают увеличить объемы, несмотря на нехватку персонала.
— За первые 10 лет внедрения системы непрерывных улучшений производительность труда выросла в разы. Сейчас средний рост производительности — порядка 5% в год. Если говорить про прошлый год, то за счет инструментов нашей производственной системы мы сократили кадровую потребность на 500 человек, — рассказывает Оксана Исакова.
Параллельно на предприятии непрерывно автоматизируют процессы. На автозаводе один из самых современных в России окрасочных комплексов, роботизированные сварочное и штамповочное производства, а с недавнего времени роботам поручена еще и логистика: в цехах работают автоматические транспортировщики, внедряются беспилотные грузовые платформы собственной разработки. Аналитика по эффективности работы оборудования тоже автоматизируется: сейчас на заводе внедряется IT-проект, благодаря которому за мониторинг оборудования будет отвечать искусственный интеллект — это помогает более эффективно распределять загрузку производственных линий и персонала. Но всё это не главное.
— Под предлогом внедрения производственных систем многие компании пытаются закрыться от большого количества проблем инвестициями в оборудование — вот сейчас купим новый станок, и всё будет хорошо. Это так не работает. Никакие передовые станки не дадут эффекта без людей. Поэтому важно вместе с внедрением новых технологий инвестировать именно в сотрудников: в их обучение, повышение квалификации, социальное благополучие, — подчеркивает Исакова.
Учиться у лидеров
Нижегородский автозавод не скрывает ни своих успехов, ни методик, которые их обеспечили, и более того, готов делиться компетенциями. По словам директора Академии современных технологий автомобилестроения им. А.Н. Моисеева (корпоративный университет автозавода) Галины Бирюковой, курс по производственной системе завода — один из самых востребованных в академии, причем не только у предприятий автопрома, но и в сфере услуг, банковском и страховом бизнесе: количество слушателей академии ежегодно растет.
— Мы заинтересованы делиться опытом, потому что во время обучения улучшаются и наши процессы. Любой, кто приходит к нам на площадку, наш ли это сотрудник или сторонний, наблюдает за нашими проблемами и дает полезные предложения. Для нас это дополнительный ресурс, свежий взгляд. И потом, когда мы обучаем своих партнеров, поставщиков, это помогает нам говорить с ними на одном языке и вместе работать над качеством, снижать себестоимость, — заключает Оксана Исакова.